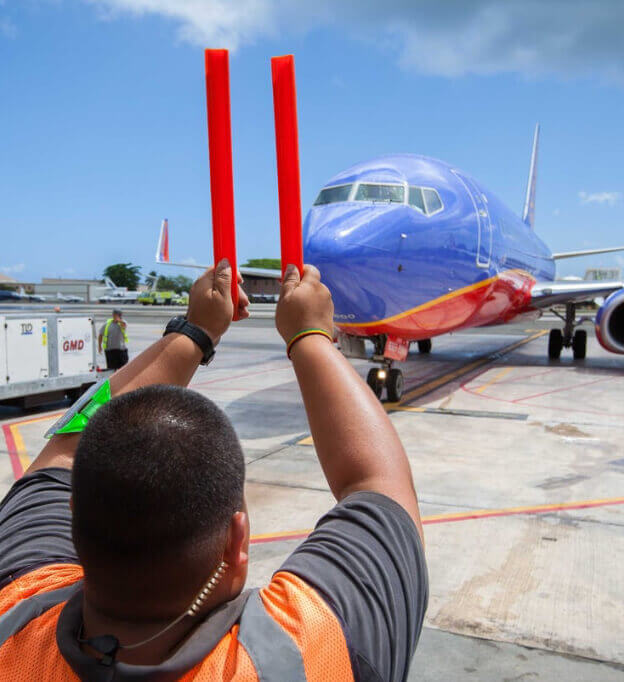
The Southwest Team on the ground, ca. today. Even though Southwest no longer turns planes in 10 minutes, it still has some of the fastest turnaround times in the industry.
A Turning Point: The Birth of the 10-Minute Turn
$143.
That’s all that was left in Southwest’s bank account in the spring of 1972. Barely enough to pay the daily wages of a single Employee, never mind get an airplane off the ground.
Southwest President Lamar Muse considered his options.
It wasn’t the first time the new airline had come up against impossible odds. After years locked in a David-and-Goliath battle with bigger airlines just to earn the right to fly, Southwest finally won its wings in a Texas Supreme Court ruling in 1971. But the legal battles had taken a toll. With Southwest financial losses reaching $1.6 million, it looked like business was going to be grounded.
Muse had one last play to keep the company afloat: Sell the fourth plane in its fleet, a Boeing 737 it had acquired in September 1971 to accommodate a stepped-up schedule. The $500,000 profit would be just enough to give the fledgling airline one more shot, but reducing the fleet created another problem.
Southwest had been offering 14 round trips a day between Dallas and Houston for about a year, and seven between Dallas and San Antonio. It had just opened new routes between Houston and San Antonio a few months prior. The fourth plane had made all that possible. Some quick calculations revealed that maintaining the schedule with just three planes meant they would have to be in and out of the gate in just 10 minutes. Could the Team on the ground pull it off?
“We can,” said Vice President of Terminal Operations Bill Franklin. “And we will.”
A seasoned industry veteran, Franklin had a reputation at Southwest as a tough, no-nonsense Leader with just enough of a rebel streak to find unconventional ways to get things done.
So what if most airlines took an hour to turn a plane? Southwest wasn’t most airlines. Franklin just needed to convince everyone the short turnaround was possible—starting with his Team on the ground. It was a do-or-die moment for Southwest, and Franklin made sure everyone knew the Company’s survival was at stake. “We’re going to do 10-minute turns with this airplane,” he said. “If you can’t do a 10-minute turn, you’re going to get fired and we’ll bring somebody else in. And if he can’t do a 10-minute turn, we’ll fire him, too. And we’ll just keep firing until we can find someone who can do it.”
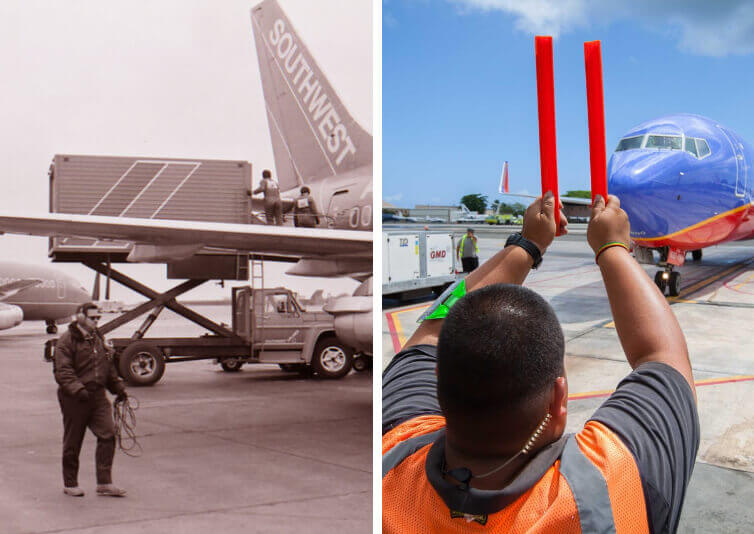
The Southwest Team on the ground, ca. 1970s and today. Even though Southwest no longer turns planes in 10 minutes, it still has some of the fastest turnaround times in the industry.
Fortunately, most members of Franklin’s Team on the ground weren’t industry veterans who’d already adopted a “that’s not the way things are done” mindset. They tackled the challenge with optimism, turning to the actions of pit crews at professional car races for inspiration and examining every step of the process to find places to shave minutes and seconds off their turn time.
What became known as the 10-Minute Turn was an all-hands-on-deck operation. In the breakroom, it often looked like a fire drill when word came in that an aircraft was arriving. Lunch pails slammed shut, conversations halted mid-sentence, and everyone raced to their posts. More than 100 tasks had to be completed before the plane could depart, and a delay in even one could derail the entire operation. This meant that nobody—not the Pilots, not the Provisioning Agents, not even Herb Kelleher himself—was above taking out the trash or restocking peanuts.
By the time the flight was boarding, the Employees at the gate had the Customers checked in and lined up for the next departure. The Flight Crew wasn’t waiting around for a cleaning crew to show up—Hostesses, as they were called, and often Pilots, were already busy tidying up the cabin. Below deck, baggage was being loaded as fast as it was coming off.
With no assigned seating, experienced Southwest Customers knew the boarding drill: Choose a seat as fast as you can, because dawdlers would be stuck with middle seats. As soon as the aircraft door closed, tug vehicles on the ground pushed it from the gate and the Pilots began to taxi—even if Customers were still figuring out where to sit. (Federal Aviation regulations put an end to that practice in 1986 when they required passengers to be seated and buckled up before the plane could leave the gate.)
People liked the rush of activity around the quick turn—it reassured them that Southwest wasn’t wasting their time. And while Teams didn’t always hit the 10-minute mark, they hit it often enough for it to become the Company’s signature move.
Even when industry regulations, increased operational complexity, and security requirements made the 10-Minute Turn impossible, Southwest still maintained some of the best turn times in the industry, and continues to work on perfecting safe, quick turns well into the 21st century.
In 2019, the airline launched the Southwest Turn Test in San Diego and Sacramento to gauge the effectiveness of new tools like handheld baggage scanners, mobile gate readers, and a communications system that enables Flight Attendants and Operations Agents to update each other in real time. Dual entry—using both the forward and rear doors for boarding and deplaning—is being tested as another way to increase efficiency. And internal “It’s Your Turn” workshops help frontline Employees understand what other Cohearts do during a turn so they can better support one another.
In 1972, the 10-Minute Turn marked a turning point for Southwest. By combining the airline’s efficiency with a historic $13 fare program, Southwest was finally able to turn the corner toward profitability.